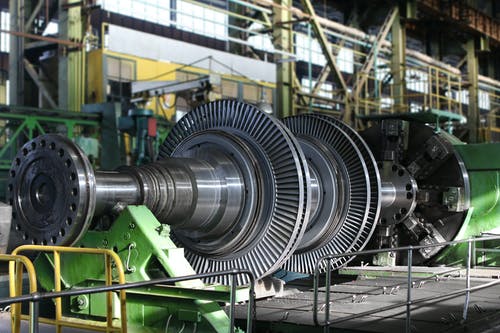
Ideas for Good Care of Heavy Equipment
September 10, 2022Heavy equipment is at the heart of the majority of industrial activities. The most effective way to reduce the chance of unexpected downtime is by performing regular maintenance on your heavy gear. Regular preventive maintenance improves efficiency and productivity and helps reduce utility bills while keeping employees and coworkers safe.
Prevention is the most important when it concerns monitoring, specifically concerning proper maintenance, as everything else may be for nothing in the event that we don’t make sure to take the necessary precautions promptly. This is essential when it comes to heavy-duty equipment, where the smallest error can lead to numerous issues.
Heavy Equipment Maintenance Tips
Inadequate maintenance decreases the life of the equipment and increases the frequency of breakdowns, increases repair costs, and reduces the speed of production. Furthermore, heavy equipment accidents take the lives of many employees each year, frequently owing to faulty maintenance and inadequate education. These tips can help to ensure the safety of employees and help prevent tragedies.
1. Keep Machine Lubricated
Heavy equipment depend on lubricants to function effectively. They help reduce damage to moving components by reducing friction. They also keep soot from collecting on the inside of the heavy machines.
Check the lubrication levels regularly for excessive grease buildup and leaks from oil seals. Always follow the manufacturer’s and the operator’s instructions on lubrication, and use the appropriate grease. When the lubricant is used insufficiently, friction and wear and tear will be increased. On the other side, excessive lubrication could result in grease accumulation and lower performance.
2. Clean Machine Regularly
The delicate parts of the equipment could be damaged by dirt and debris, which can result in expensive repairs. Metal components in heavy machinery are fitted with seals and filters to stop grime and dirt from entering the sensitive parts. So, broken seals should be replaced immediately, air ducts should be kept clean, and all filters should be regularly checked and replaced when they get filthy or blocked. Protecting the equipment inside an area from weather and dust is one of the best ways to guard against damage.
Mechanics may also develop and build specific equipment for balancing and fixing machinery as part of their maintenance services. The balancing center of these maintenance companies might provide these services as an option.
3. Perform Regular Maintenance
It’s not enough to check on and fix the equipment right now and then. Create a maintenance plan and adhere to it. Record how often every piece of equipment must be inspected for potential issues and repaired and maintained. Maintenance should be carried out frequently, and every equipment part should be inspected thoroughly. Compiling a detailed checklist is one way to ensure you don’t miss anything.
You can also utilize the services of a business that specializes in the upkeep of heavy machinery. When it comes to finding and fixing machine problems, condition based predictive maintenance companies utilize the most cutting-edge computer analysis and cutting-edge technologies available.
4. Check for Wear and Tear
Unsafe operating practices, accidents, the environment, and age-related wear and wear. Despite all precautions, machine components will age. It’s common for belts or belts that wear and seal to dry and bolts and seals to become bent or stretched. This is why it is essential to inspect all aspects of the gear.
Along with mechanical parts, inspect wiring and electronics. Extended usage, vibrations from damaged belts and gears, and environmental conditions like dust and water can damage covered circuits and wires. You should also periodically inspect the alternators, starters, and other electrical equipment.
If low-speed balancing is not used to relieve vibration problems, there is a possibility that mechanical failure may occur. You may browse the internet for companies that provide rotor balancing services, or you can ask individuals you know for suggestions.
5. Train Employees
Untrained employees can lead to injuries, equipment malfunctions, or wear. Training your staff is the most effective way to ensure that your equipment operates according to pre-determined guidelines. Local, state, and federal laws may require qualified and well-trained staff to operate heavy machinery.
Ensure your personnel knows the operation of heavy equipment and the emergency response strategy and safety measures. Training isn’t a one-time thing. In time, abilities deteriorate, workers go, and equipment is upgraded. Make sure to update and refresh operators’ skills and knowledge frequently.